Sludge sources in steel plant, and how to deal that by briquette machine
The steelmaking industry is a big source of energy, resource consumption and pollutant emissions. It is inevitable that there will generate the solid waste like fly ash, sludge, etc in the steelmaking process.
In the blast furnace-converter steel production process, the amount of iron-containing dust is about 10% of the steel output. These dust can be easily dealt with by the sludge briquete machine and back the blast furnace for recycling.
Sludge sources
Most of the sludge in steel plant comes from the processes follows: sintering, blast furnace ironmaking, steel making, rolling steel, etc. It contains elements like iron, carbon, zinc, etc. And iron, the major element we want to recycle, generally has content from 30% to 70%. This makes it a valuable waste to be recycled and generate more value for us.
Specific sludges
- Sludge from sintered dust, sinter machine head ash (8-25kg for each ton of the product, about 2% of the whole sludge)
- Sludge from blast furnace dust, mainly include gravity dust and dust collection bag ash (20-30kg for each ton of the iron, about 51% of the whole sludge)
- Sludge from converter dust, mainly include LT sludge and OG sludge (8-20kg for each ton of steel, about 22% of the whole sludge)
- Sludge from electric furnace dust (10-20kg for each ton of steel, about 6% of the whole sludge)
- Sludge from the rolling steel process, rolling steel or may call iron oxide skin (about 19% of the whole sludge)
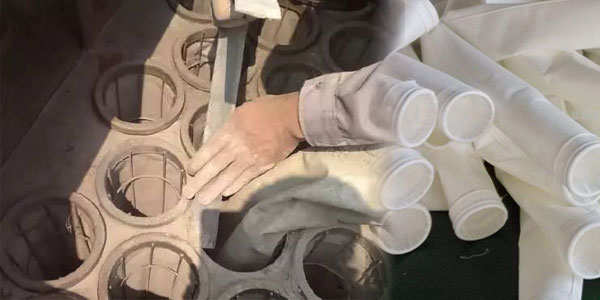
Main composition of sludge in steel plant % (reference only)
TFe | CaO | MgO | SiO2 | Al2O3 | C | ( Na + K) O | ZnO | |
sinter machine head ash | 28-55 | 2-9 | 0-1 | 3-6 | 1-3 | 0.5-2.5 | 6-15 | 0-1.5 |
gravity dust | 36-53 | 2-3 | 0.5-1 | 5-9 | 2-4 | 15-34 | 0.3-1.2 | 0.2-0.5 |
LT dust | 59-64 | 12-17 | 1.5-2 | 2-4 | 0.5-1.5 | 1-2 | ||
OG sludge | 54-61 | 14-18 | 2-7 | 1-4 | 0-3 | 2-3 | ||
electric furnace dust | 35-45 | 13-15 | 5-7 | 1-2 | 5-7 | 1-2 | 2-4 |
Use briquette machine to make sludge briquette – three ways
Sludge briquette making – use briquette as slagging flux, coolant
The sludge slagging flux briquettes use the by-product like fly ash, mill scale as raw material to make briquette instead of original slagging flux. Mix the sludge with other slagging material, some binder and turn it to briquette will make it an efficient slagging flux.
The briquette is used in the converter as slagging flux and coolant. Compare to using raw material, the briquette can get higher rocovery rate of iron, better cooling effect, and reduce the energy comsumption and raw material cost.
According to the studies, it will reduce the smelting time, the oxygen consumption, the mill scale consumption and quicklime consumption.
Solution for making sludge briquette as slagging flux, coolant.
Sludge briquette making – use sludge briquette in rotary hearth furnace
Use the iron-contained sludge follow the same way on briquetting by mixing with other different materials. Briquette them with binder, and use the briquette after drying.
The rotary hearth furnace is heated by the gas to temperature up to 1,300 celsius. In this heating process, the iron oxide, zinc oxide reduction step by step, and output after one rotation. The gas-burned hot air around temperature 1200 Celsius, which is mixed with volatilized Zinc vapor and exhaust dust. It then transported by the dust removal pipe to the heat exchanger. Volatile Zn vapor is finally cooled and collected along with the exhaust dust as zinc fine powder.
This is a way to use the briquette as the cold melt, and with high recycle rate of zinc element.
Solution for making sludge briquette for rotary hearth furnace.
Sludge briquette making – use sludge briquette in shaft furnace
The shaft furnace is similar to blast furnace: the charge input from the top of the furnace, add coke as the skeleton and reducing agent. Hot air and oxygen enrichment guarantee the smelting temperature. Only the treat material turns into metallurgical solid waste like iron-containing sludge.
Iron-containing sludge mix with cement, water, etc, and is made to briquette. After drying, the briquette gets enough strength, then is added to the furnace with other material like iron scrap, coke, etc. for smelting. The smelting process is similar to that of blast furnace.