Aluminum Dross Recycling Briquette Press Machine And Process
By using an aluminum dross briquette machine, we start a way to recycle this waste as a valuable source like other industrial waste, as well as a protection for the world’s environment today.
What is aluminum dross briquette
Use briquette machine to make briquette is a kind of way in aluminum dross circulation. This method is with low investment and quick effect. It is a reasonable utilization of the drossing treatment of aluminum ash.
Why make aluminum dross briquette
The converter molten steel should be refined. No matter which kind of refining processes we have chosen, after the molten steel output from the converter, the modification of the top flux is necessary.
Aluminum-based modifier is suitable for this usage. The aluminum element is used as a deoxidizer to adjust the physical and chemical properties by deoxygenating for the molten steel as well as the converter flux.
Other materials are also added in the briquette to make the briquette with other functions of adjusting the alkalinity and viscosity, etc.
The aluminum dross sources
Aluminum dross (other names as aluminum ash or aluminum slag) is a kind of solid waste from the aluminum making process.
Mainly there are three of it:
- In the process of producing aluminum by molten salt electrolysis, a certain amount of aluminum dross will be produced due to the operation and measurement of the carrying, anode replacement, aluminum ouput, and ingot casting, one ton aluminum oxide will produce about 30 to 50 kg of aluminum dross;
- During the casting process, aluminum will also produce aluminum ash due to ingot casting, multiple remelting, alloy preparation, component casting, or forging, extrusion, rolling, and cutting. The process produces aluminum dross for about 30 to 40 kg per ton product ;
- Aluminum dross will also be produced during the process of recycling aluminum scrap. The recovery rate of scrap aluminum recycled and reprocessed into products is generally 75% to 85%. Recycling one ton aluminum dross will produce more than 100 kg extra aluminum dross.
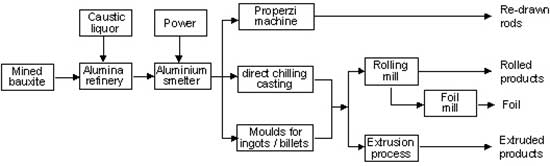
Make aluminum dross as a flux modifier
Use an aluminum dross briquette machine can turn this material to briquette for further usage.
The aluminum dross should be mixed with other materials and additives and then make the briquette. Normally, the briquette is used as flux modifier in furnace (the aluminum-based modifier).
Aluminum dross briquette press machine
The hydraulic roller briquette press is used to make aluminum dross briquette.
Hydraulic roller briquette press is a kind of briquette machine with easy pressure adjustment system. Thanks to the high pressure, materials can be briquette with a very low moisture.
In the aluminum dross briquetting process, Maxton prepares high quality and standard roller material which serves with long life.
Process of aluminum dross flux briquette making
Before making the briquette, the aluminum dross should be mixed with other materials (like quicklime, etc) with proper rate, then the briquette can be made by the briquetting machine.
General process as follow
Raw material ⇒ Crushing ⇒ Mixing ⇒ Briquette
Raw materials first are crushed to get a certain size range.
After crushing, materials input to the mixer with a proper rate, there in the mixer (wheel mill), these materials are stired and pre-compressed, make the material with proper size and reduce the gaps between the particles, further improve the quality of briquette.
The briquette making under a suitable pressure, raw material come through the briquette press and output by briquettes with suitable size.
Things should pay attention to improve your briquetting work
Iron removal
In order to prevent damage to the system from iron, an installation of iron removal device is more reasonable, which will help to increase wear resistance and fatal damage (large iron)
Conveying system
The addition of the ration silo in the middle of the whole conveying system can ensure a uniform transportation of the raw material, prevent damage of the briquette machine (roller, motor, etc.). Due to the instability of the feeding, it will reduce the excessive energy loss and decline of finished product.
Rate and size of raw materials
The size of raw materials should be controlled in a certain range for a better briquette performance. Different material can be in different size ranges. The material in big size with small amount acts as a skeleton of the briquette.
The briquette storage packing
There are many types of packing machines, like the powder filler machine, liquid packing machine, and solid packing machine, but in briquette making process, the best choice for us is an exact packing machine named tons packer for our large capacity and usage.
Due to the characteristics of the briquette, long-term storage is prone to chalking, seal the product or pack it with packing machine will multiples the storage time.